Manipulator Robotics Introduction
Notes of book Introduction ot Robotics Mechanics and Control.
Content
Focus on mechanical manipulator type of robot.
Table of content
- Introduction
- Describe pose in 3D
- Position & rotation
- Attach a coordinate system or frame to an object, then describe its pose w.r.t other reference coordinate systems
- Geometry of mechanical manipulators. Static Kinematics
- Manipulator
- consist of rigid links, which are connected by joints
- joint angles (rotation), joint offset (translation)
- tool frame is attached to end-effector
- base frame is attached t o nonmoving base of manipulator
- Kinematics
- Treats motions without regard to the forces which cause it
- Study time-based properties of the motion
- Forward kinematics of manipulator
- Given a set of joint angles, compute the pose of tool frame w.r.t the base frame
- Inverse kinematics of manipulator
- Given the pose of end-effector of the manipulator, calculate all possible sets of joint angles
- non-linear optimization problem
- Manipulator
- Kinematics with velocities and static forces
- Jocobian of manipulator
- mapping from velocities in joint space to Cartesian space
- singularity of the mechanism
- mechanism become locally degenerate and behaves as if it only has 1 DoF
- Jocobian of manipulator
- Manipulator dynamics
- Study forces required to cause motion
- Motion of manipulator. Trajectory in space
- Trajectory generation
- spline: refer to a smooth function and passes through a set of via points
- Trajectory generation
- Mechanical design
- How to design a manipulator, including its mechanical structure, attached sensors
- linear/non-linear control theory
- actuator perform torque on the joint
- position and velocity sensors are monitored by control algorithm
- linear control
- linear approximations to the dynamics of a manipulator
- non-linear control
- consider nonlinear dynamics
- Active fore control
- Force control vs position control
- Programming robots
- Off-line simulation
Notation
- $A$: vector or matrix
- $a$: scalars
- $^A P$: position vector under coordinate system {A}
- $^A_B R$: rotation matrix {B} relative to {A}. $$^A P = ^A_B R ^B P $$
- Vectors are taken to be column vectors
Spatial Descriptions and transformations
- Position under universal coordinate frame {A}. $^A P$
- $^A P_{BORG}$ is the vector from frame {A} to frame {B} origin, and expressed under frame {A}
- Rotation matrix (3x3), frame {B} relative to frame {A}
$$
^A_B R = [^A \hat{X}_B, ^A \hat{Y}_B, ^A \hat{Z}_B]
$$
where $^A \hat{X}_B, ^A \hat{Y}_B, ^A \hat{Z}_B$ are the coordinate of unit axes vectors of frame {B} in frame {A}. Row vectors are the axes vectors of frame {A} in frame {B} since $^B_A R = ^A_B R^{-1} = ^A_B R^T$
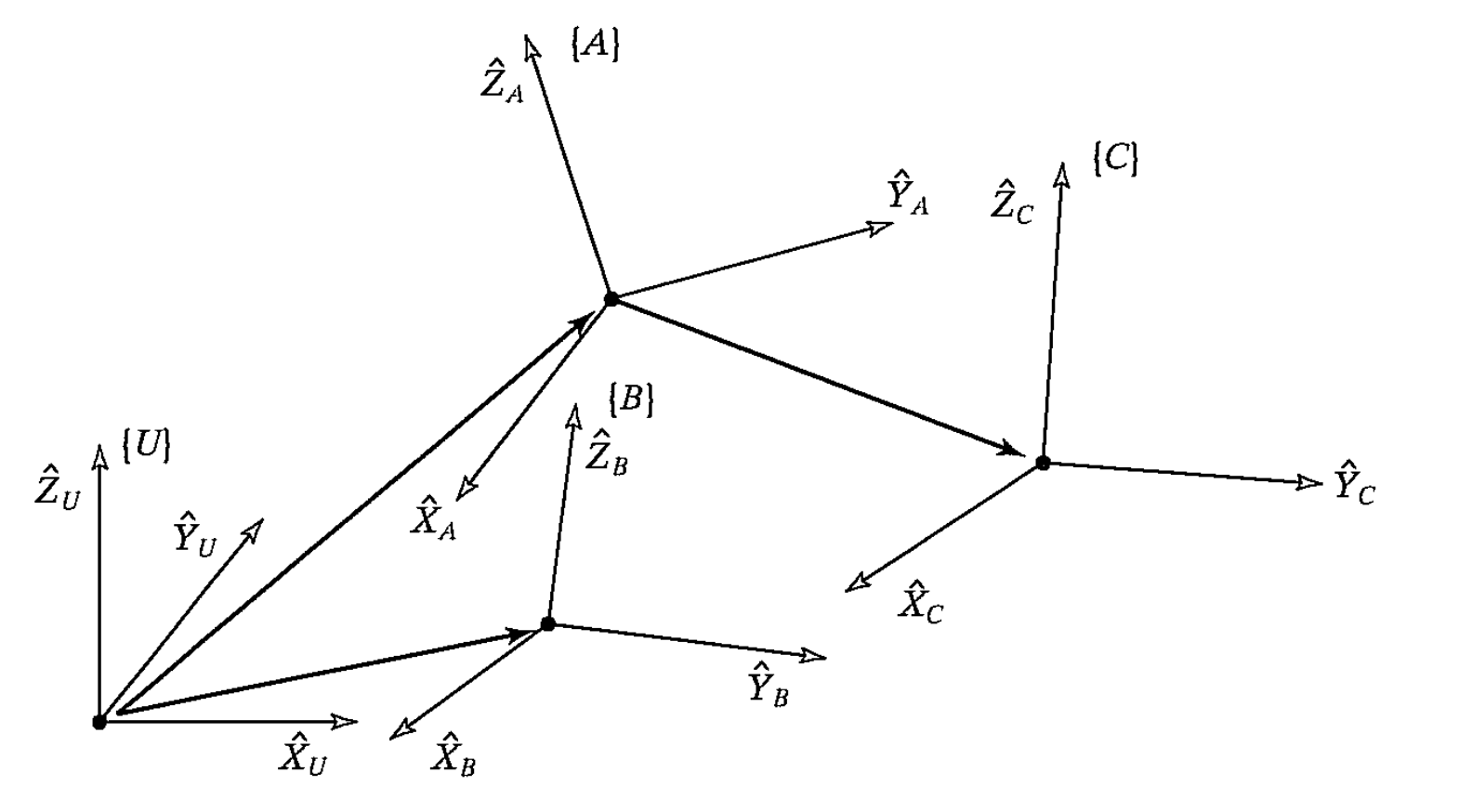
- Maps position from frame {B} to frame {A}
$$
^A P = {^A_B R} {^B P} + ^A P_{BORG}
$$
or in homogenous coordinate, write as $^A_B T$ - Transformation operators. Not transforming the frame, move the point under the same frame instead
$$
^A P_2 = T {^A P_1}
$$
The transform that rotates by $R$ and translate by $Q$ is the same as the transform that describes a frame rotated by $R$ and translated by $Q$ relative to the reference frame. - Other rotation forms
- 3 rotations taken about fixed axes (fixed-angle sets) yield the same final orientation as the same three rotations taken in opposite order about the axes of the moving frame (Euler-angle sets).
- Equivalent angle-axis representation $R_K(\theta)$. Rotating around unit vector $^A \hat{K}$ by $\theta$
- Euler parameters. Unit quaternion
- Different vectors
- line vector: dependent on its line (or point) of action to cause its effect
- free vector: only its direction and magnitude matters, can be placed in anywhere in space
- Reduce computation
- Compare matrix calculations vs matrix vector calculations
- Calculate first 2 columns, use cross product to get the third column
Manipulator Kinematics
Joints, Links
- joint axis: revolute or prismatic
- joint 1 is the first movable joint in the robot
- joint n is the last movable joint in the robot
- link: the arm. link $i$ is from axis $i$ to axis $i+1$
- link 0 is from the non-moving base of the robot to the first movable joint
- link n is from the last movable joint to the end-effector
- link length: length of line which is perpendicular to the 2 axes (mutual perpendicular, current axe and next axe)
- $a_i$ = distance from $\hat{Z}_i$ to $\hat{Z}_{i+1}$ measured along $\hat{X}_i$
- $a_0 = 0$ because axis joint $0$ could be chosen arbitrary
- $a_n = 0$ because there is no more other joints behind
- link twist: angle in the projected plane from axis $i$ to axis $i+1$. The plane’s normal vector is $a_i$, the angle follows the right-hand law
- $\alpha_i$ = angle from $\hat{Z}_i$ to $\hat{Z}_{i+1}$ measured about $\hat{X}_i$
- $\alpha_0 = 0$ because axis joint $0$ could be chosen arbitrary
- $\alpha_n = 0$ becaus there is no more other joints behind
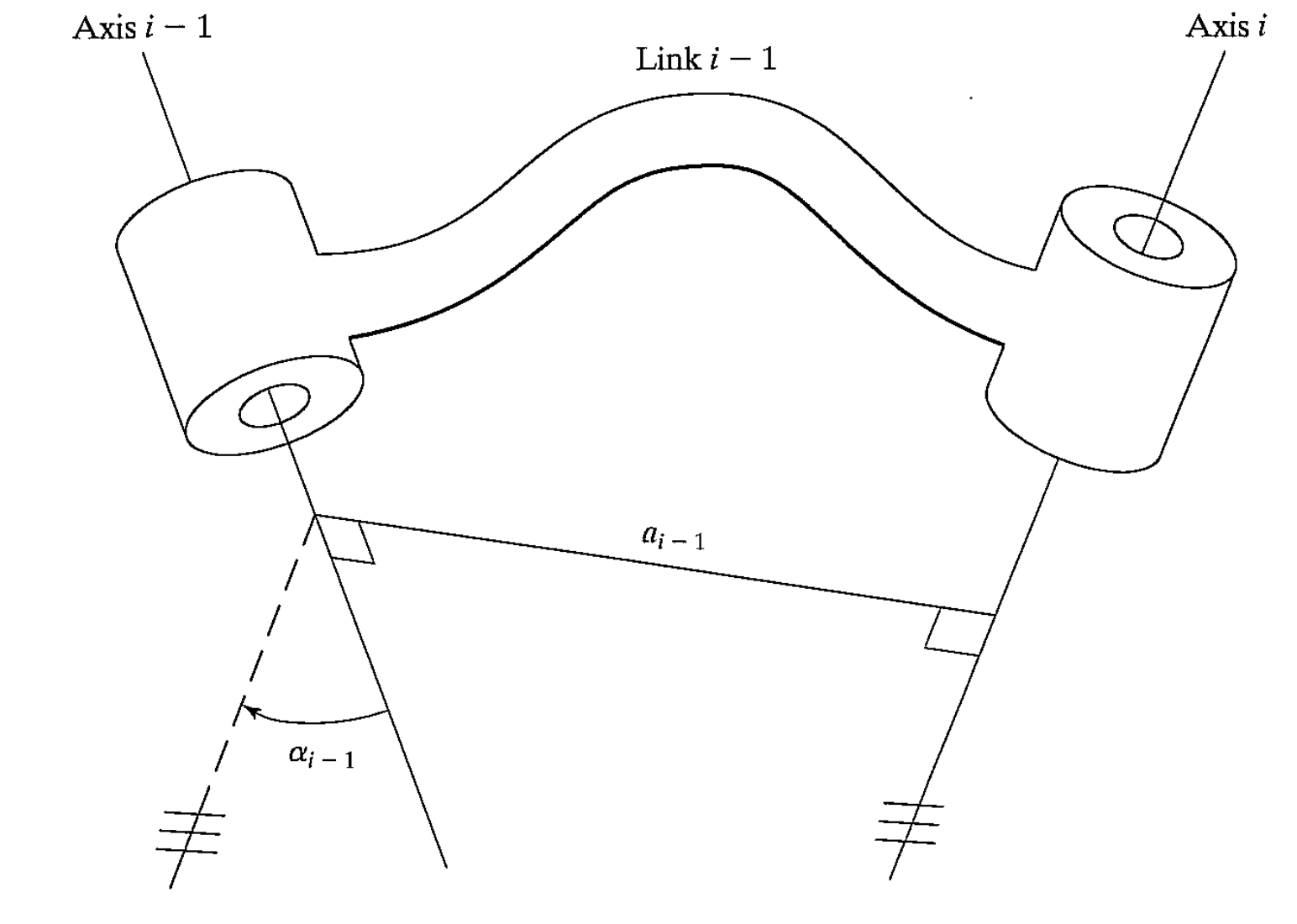
- link offset: distance between intersection of $a_{i-1}$ on axis $i$ and $a_i$ on $i$. Distance is measured along the axis $i$
- $d_i$ = distance from $\hat{X}_{i-1}$ to $\hat{X}_i$ measured along $\hat{Z}_i$
- $d_1$
- $d_1 = 0$ for revolute joint
- $d_1$ zero position could be chosen arbitrary for prismatic joint
- $d_n$ same as above
- joint angle: angle between from $a_{i-1}$ to $a_i$ around axis $i$. Also follows right-hand law
- $\theta_i$ = angle from $\hat{X}_{i-1}$ to $\hat{X}_i$ measured about $\hat{Z}_i$
- $\theta_1$
- $\theta_1$ zero position could be chosen arbitrary for revolute joint
- $\theta_1 = 0$ for prismatic joint
- $\theta_n$ same as above
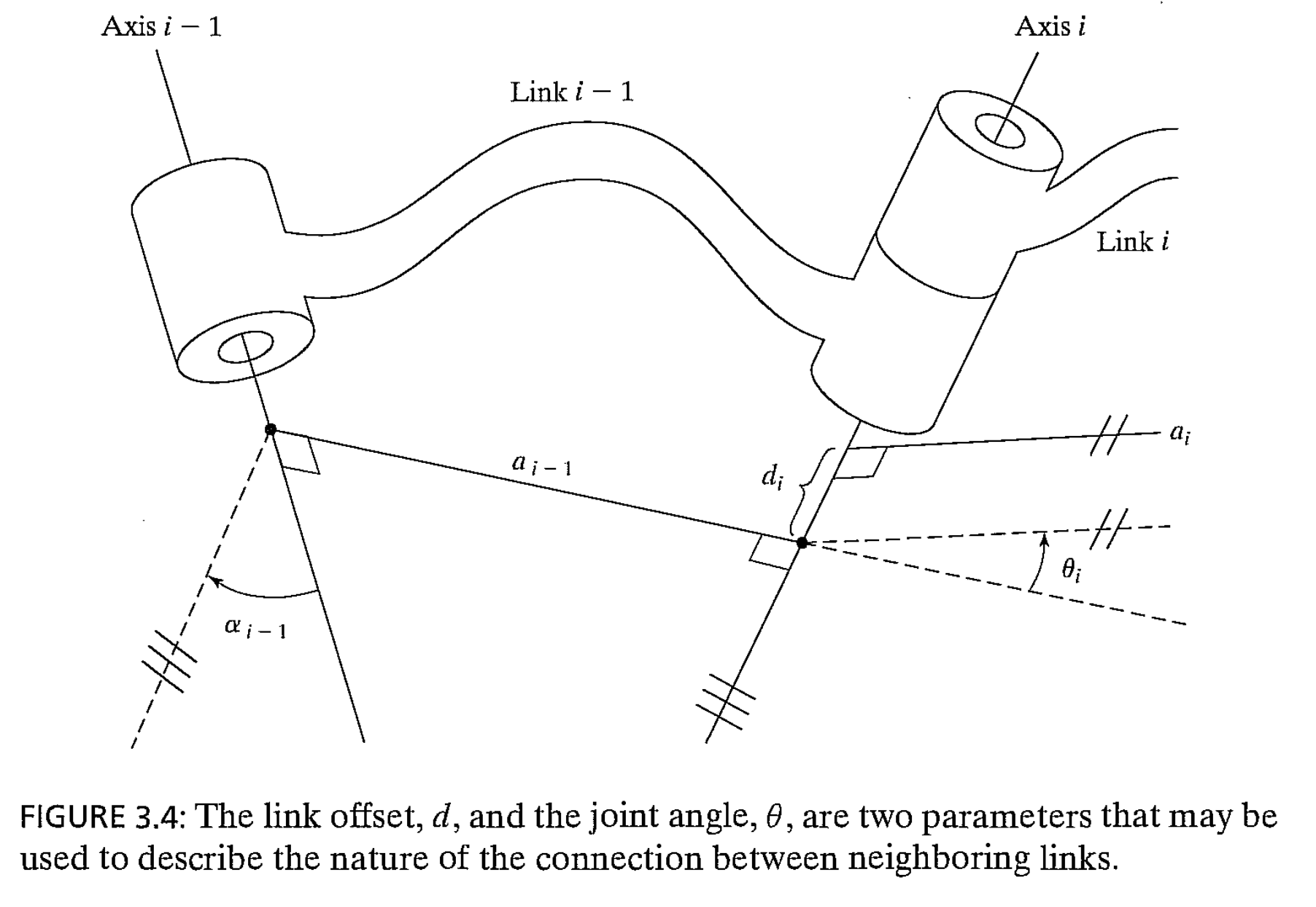
- link parameters: 3 fixed parameters
- joint variable: 1 changeable parameter
- $\theta_i$ for revolute joint i
- $d_i$ for prismatic joint i
Frames
- frame {i} attach to link i (axis i)
- Origin is the intersection point of the common perpendicular line on axis $i$.
- Z-axis coincident with joint axis i
- X-axis points along $a_i$ in the direction from joint $i$ to joint $i+1$
- or orthonormal to the $Z_i, Z_{i+1}$ plane
- Frame {0} is arbitrary, but usually chose coincides with frame {1}. Frame {0} is the one stationary and serve as reference frame
- Frame {n}
- X-axis is chosen it aligns with X-axis of frame {n-1} when $\theta_n = 0$
- Origin is chosen at axis $n$ when $d_n = 0$
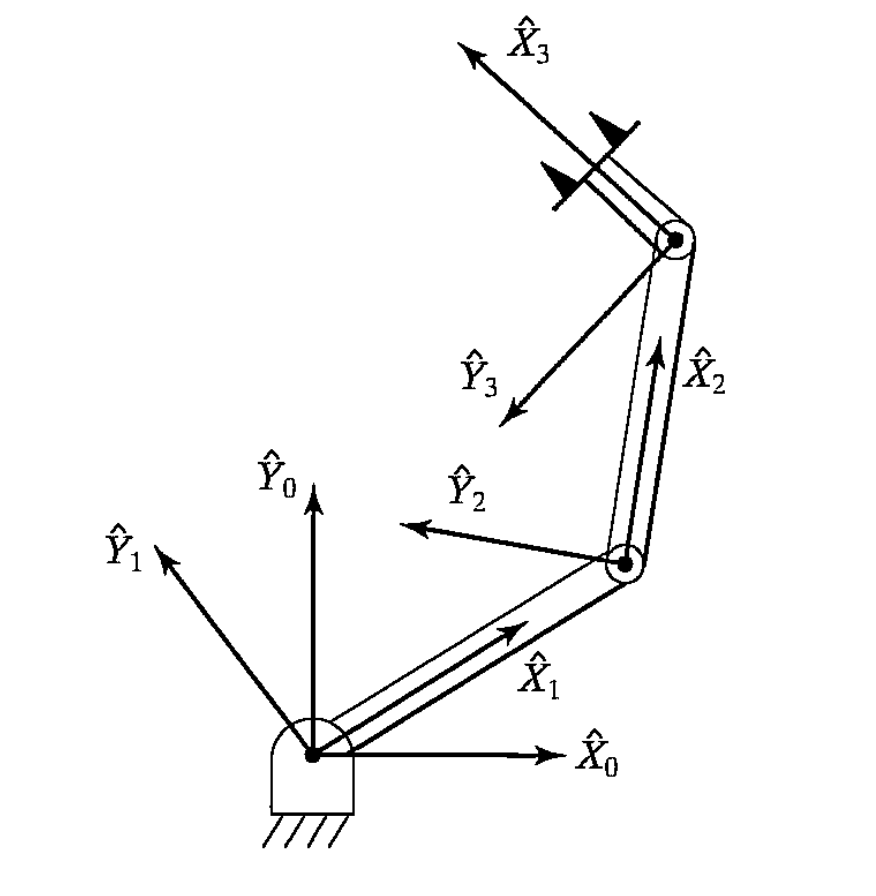
- Frame naming convention
- Base frame {B}: frame {0}, link {0}, nonmoving
- Wrist frame {W}: frame {N}, last link the manipulator. Refer as $^B_W T = ^0_N T$
- Tool frame {T}: the end of any tool held by robot, or in the middle of fingertips. Refer as $^W_T T$
- Station frame {S}: task-relevant location, task frame, world frame, universal frame. Refer as $^B_S T$
- Goal frame {G}: location to which the robot is to move the tool. Tool frame and Goal frame will coincident in the end. Refer as $^S_G T$
- WHERE function
- $^S_T T = ^B_S T^{-1} {^B_W T} {^W_T T}$, present where the tool is relative to the station
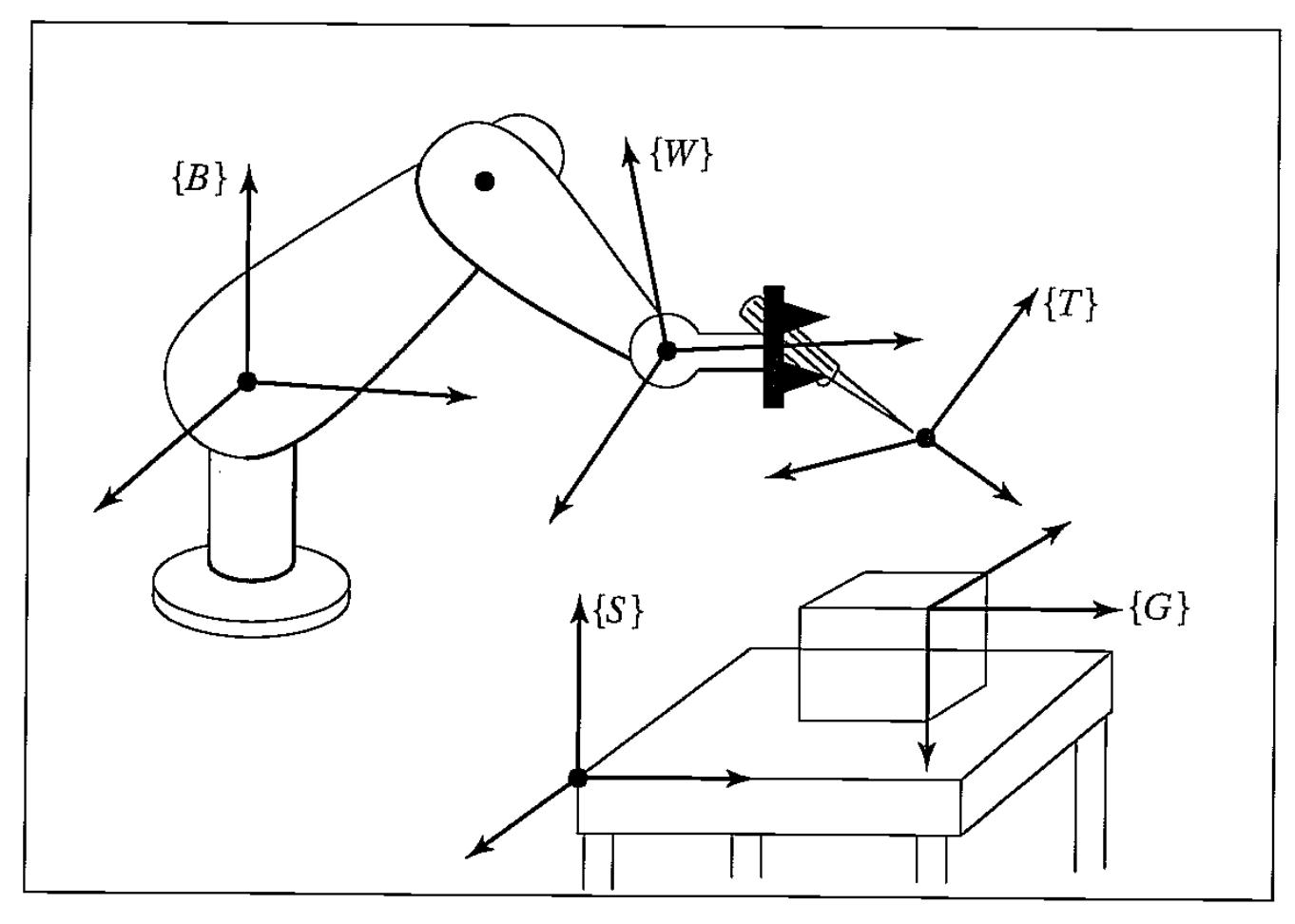
- Frame kinematics transformation
$$
^{i-1}_i T=\begin{bmatrix}
\cos\theta_i & -\sin\theta_i & 0 & a_{i-1} \\
\sin\theta_i \cos\alpha_{i-1} & \cos\theta_i \cos\alpha_{i-1} & -\sin\alpha_{i-1} & -\sin\alpha_{i-1}d_i \\
\sin\theta_i \sin\alpha_{i-1} & \cos\theta_i \sin\alpha_{i-1} & \cos\alpha_{i-1} & \cos\alpha_{i-1} d_i \\
0 & 0 & 0 & 1
\end{bmatrix}
$$
$$
^0_N T = {^0_1 T} {^0_1 T} \cdots {^{N-1}_N T}
$$ - $^0_N T$ is a function of $n$ joint parameters
- Difference spaces
- actuator space: the parameters of actuators
- joint space: the space of the $n\times 1$ joint vector formed by $n$ joint variables
- Cartesian space: the relationship between different frames
- Reduce computation
- Store sin cos values into lookup table
- Store intermediate variables
Inverse Manipulator Kinematics
- What to solve: find the required joint angles to get the required $^S_T T$
- $^B_S T, ^W_T T$ are known
- Find required joint angles to get the required $^B_W T = ^0_N T$
- Workspace: the volume of space that end-effector of manipulator can reach
- Dextrous workspace: volume of space that end-effector can reach with all orientations
- Reachable workspace: volume of space that end-effector can reach in at least one orientation
- But we usually care about the workspace of wrist frame {W} instead of the end-effector tool frame {T} since $^W_T T$ is known
- Workspace is a subset of the n-DoF subspace, where subspace is the reachable workspace without constraints of parameters
- Solvable of inverse Kinematics
- Solution existence = desired position and orientation of wrist frame {W} is in the workspace
- Multiple solutions = desired position and orientation of wrist frame {W} is in the Dextrous workspace
- 6 DoF manipulator could have up to 16 possible solutions
- Proved: all systems with revolute and prismatic joints having 6 DoF in a single series chain are solvable
- But solution is in numerical
- Closed-form solutions of 6 DoF is solvable in special cases
- e.g. 3 neighboring joint axes intersect at a point
- Method of solution
- numerical solutions: iterative method, slow, not guaranteed to find all solutions
- closed-form solutions
- construct the desired $^B_W T$ matrix (subspace) according to the required position and orientation
- construct equations between the constructed $^B_W T$ and kinematics matrix
- replace sin cos with single variable $u$, to convert transcendental equations to polynomial equations
- Proved. Polynomials up to degrees 4 could be solved in closed form
- forms triangles
- Special cases
Pieper’s solution
- Any 3 DoF manipulator’s closed-from solution can be solved
- Compute a modified goal frame $^S_{G\prime} T$ such that $^S_{G\prime} T$ lies in manipulator’s subspace and is “near” to $^S_G T$
- Compute inverse kinematics for $^S_{G\prime} T$
Pieper’s solution to get closed-form solution
- Solve for first 3 joints given the position of the origin of frame {4} {5} {6}
- Solve for the later 3 joints given the orientation
Jocobians: velocities and static forces
Linear and angular velocities
- Linear velocity vector for a point
$$
^A(^B V_Q) = {^A_B R} {^B V_Q} = \frac{^A d}{dt} {^B Q} = {^A_B R} \lim_{\Delta t \rightarrow 0} \frac{^B Q(t+\Delta t) - {^B Q(t)}}{\Delta t}
$$
is the velocity of position vector Q whose differentiation is done in frame {B} and finally expressed in frame {A}. - Short write cases
- $v_c = {^U V_{CORG}}$ is the velocity of origin of frame {C} differentiation in reference frame {U}
- $^A v_c$ is the above velocity but expressed in frame {A}
- Angular velocity vector for a body
$$
^C ({^A \Omega_B})
$$
is the rotation of frame {B} relative to frame {A}, and finally expressed in frame {C}- The direction of vector is the rotation axis
- The magnitude of vector is the current speed of rotation
- Short write cases
- $w_c = {^U \Omega_C}$ is the angular velocity of frame {C} relative to reference frame {U}
- $^A w_c$ is the above angular velocity but expressed in frame {A}
Simultaneous linear and rotational velocity
$$
^A V_Q = {^A V_{BORG}} + {^A_B R} {^B V_Q} + {^A\Omega_B} \times {^A_B R} {^B Q}
$$- where frame {A} is the reference frame and fixed
- frame {B} has both linear velocity $^A V_{BORG}$ and rotational velocity $^A \Omega_B$
- point Q also has a linear velocity $^B V_Q$ in frame {B}
Velocity of link i is given by vector $v_i$ and $w_i$, which are gotten relative to frame {0} and can be expressed in any frame
velocity propagation: velocity of link i+1 is velocity of link i, plus new velocity components added by joint i+1
$$
\begin{aligned}
^{i+1} w_{i+1} &= {^{i+1}_i R} {^i w_i} + \dot{\theta}_{i+1} {^{i+1} \hat{Z}_{i+1}} \\
^{i+1} v_{i+1} &= {^{i+1}_i R} ({^i v_i} + {^i w_i} \times {^i P _{i+1}} )
\end{aligned}
$$where
- $\dot{\theta}_{i+1} {^{i+1} \hat{Z}_{i+1}} = ^{i+1} \begin{bmatrix} 0 \\ 0 \\ \dot{\theta}_{i+1} \end{bmatrix}$
- $^i P_{i+1}$ is the coordinate of origin of frame {i+1} in frame {i}
$$
\begin{aligned}
^{i+1} w_{i+1} &= {^{i+1}_i R} {^i w_i} \\
^{i+1} v_{i+1} &= {^{i+1}_i R} ({^i v_i} + {^i w_i} \times {^i P _{i+1}} ) + \dot{d}_{i+1} {^{i+1} \hat{Z}_{i+1}}
\end{aligned}
$$where $\dot{d}_{i+1} {^{i+1} \hat{Z}_{i+1}} = ^{i+1} \begin{bmatrix} 0 \\ 0 \\ \dot{d}_{i+1} \end{bmatrix}$
Velocity transformation
$$
\begin{aligned}
^A v_A &= {^A_B T_v} {^B v_B} \\
\begin{bmatrix}
^A v_A \\
^A w_A
\end{bmatrix}
&=
\begin{bmatrix}
^A_B R & {^A P_{BORG}} \times {^A_B R} \\
0 & {^A_B R}
\end{bmatrix}
\begin{bmatrix}
^B v_B \\
^B w_B
\end{bmatrix}
\end{aligned}
$$
Jocobian
- Equation
$$
^0 v = {^0 J(\Theta)} \hat{\Theta}
$$
where- $^0 v = \begin{bmatrix} {^0 v} \\ {^0 w} \end{bmatrix}$ is the Cartesian velocities of the link n expressed in frame {0}
- $\hat{\Theta}$ is the vector of joint velocity
- ${^0 J(\Theta)}$ is the Jocobian matrix, which represents the derivate of each term of Cartesian position and orientation on each term of joint angle. Its value changes as the joint angles change.
- Changing frame
$$
{^A J(\Theta)} = \begin{bmatrix}
{^A_B R} & 0 \\
0 & {^A_B R}
\end{bmatrix}
{^B J(\Theta)}
$$ - Inverse of the Jocobian could be used to calculate joint velocities given desired Cartesian velocities of link n
- Singularities: where the joint angles make the ${^0 J(\Theta)}$ singular
- Workspace-boundary singularities: manipulator fully stretched out or folded back
- Workspace-interior singularities: caused by a lining up of 2 or more joint axes
Force and torque
- Force propagation from link to link
$$
\begin{aligned}
^i f_i &= {^i_{i+1} R} {^{i+1}} f_{i+1} \\
^i n_i &= {^i_{i+1} R} {^{i+1}} n_{i+1} + {^i P_{i+1}} \times {^i f_i}
\end{aligned}
$$
where- $f_i$ is force exerted on link i by link i-1
- $n_i$ is torque exerted on link i by link i-1
- Torque for joint
- For revolute joint
$$
\tau_i = {^i n_i^T} {^i\hat{Z}_i}
$$ - For prismatic joint
$$
\tau_i = {^i f_i^T} {^i\hat{Z}_i}
$$
- For revolute joint
- Jocobian
$$
\tau = {^0 J^T} {^0 \mathcal{F}}
$$
where $\mathcal{F}$ is the Cartesian forces acting at the hand, and $\tau$ is the joint torques - Force transformation
$$
\begin{aligned}
^A \mathcal{F}_A &= {^A_B T_f} {^B \mathcal{F}_B} \\
\begin{bmatrix}
^A F_A \\
^A N_A
\end{bmatrix}
&=
\begin{bmatrix}
^A_B R & 0 \\
{^A P_{BORG}} \times {^A_B R} & {^A_B R}
\end{bmatrix}
\begin{bmatrix}
^B F_B \\
^B N_B
\end{bmatrix}
\end{aligned}
$$
and
$$
{^A_B T_f} = {^A_B T_v^T}
$$
Trajectory generation
- Motions is tool frame {T} relative to station frame {S}
- To generate a trajectory of motions
- Spatial constraints: Path points
- a set of intermediate frames that the tool frame should reaches
- including initial, target point, and via points
- Temporal attributes: the time between points
- Spatial constraints: Path points
- In order to make the trajectory smooth, the function of the trajectory and its first derivate should be continuous
- Convert path joints to joint angles by inverse kinematics
- For each 2 path points, fit a function of the joint angles
- Cubic polynomial
- 4 entries since each 2 path points provides 4 constraints (2 position constraints, 2 velocities constraints)
- $\theta(t) = a_0 + a_1 t + a_2 t^2 + a_3 t^3$
- Constraints of each 2 point
$$
\begin{aligned}
\theta(t_0) &= theta_0 \\
\theta(t_1) &= theta_1 \\
\dot{\theta}(t_0) &= v_0 \\
\dot{\theta}(t_1) &= v_1
\end{aligned}
$$ - Higher-order polynomials
- Quintic polynomial (5 degree, 6 entires), enabling specify position, velocity, and acceleration.
- Linear function with parabolic blends
Reference
- Rodd, Michael G. “Introduction to robotics: Mechanics and control: John J. Craig.” (1987): 263-264.